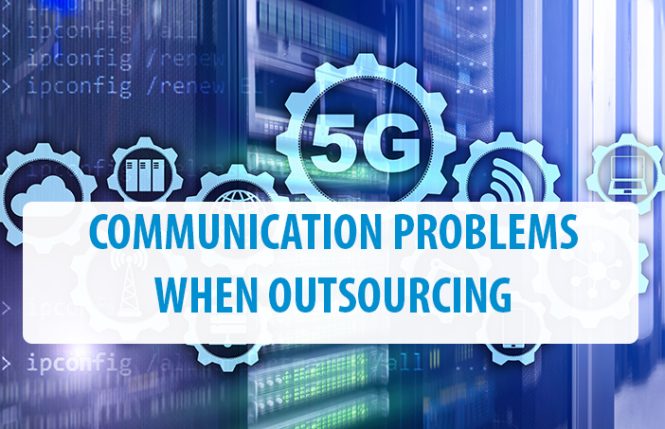
Maintaining quality control when outsourcing production presents a significant challenge for businesses today. Successfully navigating this complexity requires a strategic and proactive approach that goes beyond simple cost-cutting. Outsourcing production, while often offering substantial financial advantages, can introduce complexities in ensuring the quality of the final product. This article dives into the intricacies of quality control in outsourced production, examining the common difficulties and offering practical solutions to ensure top-notch product standards are met throughout the production process. We’ll explore the importance of establishing clear communication protocols, implementing robust quality assurance processes, and actively monitoring performance, all crucial factors in maintaining quality standards when manufacturing in a remote location. The following sections will detail these aspects of effective quality control.
Identifying the Challenges of Maintaining Quality Control in Outsourcing
Communication Gaps and Cultural Differences
Effective communication is the bedrock of any successful production process, especially when production is outsourced. Language barriers and differing communication styles between the contracting company and the outsourcing partner can create significant obstacles to effective quality control. In some cases, subtle differences in work ethic or expectations regarding quality standards can lead to conflicts or misunderstandings. It’s crucial to understand the nuances of the culture in which the manufacturing takes place, establishing clear and consistent communication protocols that accommodate these differences.
Implementing Robust Quality Assurance Processes
Developing a Clear Quality Control Plan
Establishing a meticulous quality control plan from the outset is paramount. This document should precisely outline expectations for quality standards, testing procedures, and acceptable tolerances. Specific roles and responsibilities must be defined within the outsourcing partner’s organization to clearly allocate ownership for quality control throughout the process. A well-defined quality control plan serves as the foundation for all subsequent efforts to maintain the agreed-upon quality standards.
Establishing Consistent Monitoring and Reporting Mechanisms
Monitoring Production Performance
Monitoring the progress and adherence to quality control standards is crucial for successful outsourced production. Regular audits and inspections, ideally combined with visual quality assurance and performance measurement, provide insights into the ongoing quality of the production process and serve as early indicators of potential issues. These should be conducted by trained personnel to ensure objectivity and accuracy.
Utilizing Technology to Enhance Quality Control
Leveraging Quality Control Tools
Technology plays an increasing role in enhancing quality control when outsourcing production. Tools like video conferencing, instant messaging, and project management software can help facilitate communication and track progress more effectively. Using these technologies in tandem with established quality control metrics enables the contracting company to maintain continuous oversight of the process and respond swiftly to any arising issues.
Building Strong Relationships with Outsourcing Partners
Fostering Collaboration
Strong relationships between the company and the outsourcing partner are essential. Open communication channels and mutual respect foster a collaborative environment where both parties can work together to ensure product quality. Regular meetings, shared goals, and a willingness to adapt to one another’s needs are key elements for building a successful and sustainable relationship.
Addressing Cultural Differences for Quality Control
Understanding Cultural Nuances
Outsourcing production to different countries often involves navigating cultural differences that can impact quality control. Understanding these differences in communication styles, work ethics, and expectations for quality standards is essential for building positive relationships and minimizing misunderstandings. Clear guidelines and effective communication strategies are crucial in bridging these cultural gaps.
The Role of Quality Audits in Maintaining Quality
Conducting Regular Audits
Implementing regular quality audits is crucial to guarantee the continued adherence to the agreed-upon quality standards. These audits should not only encompass visual inspection but should also include rigorous testing and measurements at various stages of production. The data collected from these audits will provide valuable insights for continuous improvement of the production process and for identifying areas for enhancement.
Addressing Communication Breakdown During Outsourcing
Utilizing Technology for Clear Communication
Effective communication channels are vital during the outsourcing process. Utilizing video conferencing platforms, instant messaging, and comprehensive project management software can bridge geographical divides and streamline communication. These tools facilitate the exchange of critical information and help promptly address any concerns or issues that may arise.
Case Study: A Successful Outsourcing Partnership for Quality Control
Company X’s Experience
In one instance, Company X successfully managed the quality of outsourced production through the implementation of a strict quality assurance program. This program involved regular audits, clearly defined roles, and frequent communication. Using a collaborative approach and open communication channels proved successful in maintaining high standards for product quality throughout the entire process. Company X, by prioritizing these aspects, demonstrated how consistent monitoring and prompt issue resolution could effectively ensure the quality of their products even when production occurred in another country or region.
Maintaining quality control when outsourcing production is a complex challenge, requiring a proactive and multifaceted approach. Understanding the inherent difficulties, such as communication gaps and cultural differences, and proactively addressing them through clear communication protocols, robust quality assurance processes, and dedicated oversight is crucial. By embracing technology, fostering strong relationships, and implementing transparent reporting mechanisms, businesses can significantly improve their chances of success in maintaining quality standards when outsourcing. The key is to view outsourcing as a partnership and not just a cost-cutting measure. A well-defined plan, coupled with continuous monitoring and refinement, allows businesses to reap the benefits of outsourcing while maintaining the quality standards that drive customer satisfaction and brand loyalty. Moving forward, companies should commit to investing in effective communication tools, quality audits, and collaborative relationships to ensure consistent high-quality outcomes. This will not only benefit the clients but also facilitate growth and success for the outsourcing partner.